AIRCRAFT 101
Aircraft Noise Sources
Background
Contrary to popular perception, aircraft noise is not solely produced by an airplane's engine(s). Instead, it is a complex combination of primary and secondary sources which all contribute to the noise emitted by an aircraft in flight.
As a plane flies, it pushes through the air, disturbing the smooth fluid flow of air molecules much like a boat creates a wake moving through the water. This wake is the result of the interaction of the air molecules with the aircraft's fuselage, wings, tail, and engines which creates friction. The air friction generates turbulent airflow and drag, which manifests itself as noise.
When planes land they extend their landing gear and flaps to slow down and prepare for landing, this action increases the air friction and dramatically increases the turbulent airflow around the airplane, which produces additional noise.

Jet engine noise is created by the sound of the engine's moving parts and by the sound of air being expelled at high speed. Most of the engine noise comes from the exhaust or jet behind the engine as the high-speed air from the combustion process mixes with the low-speed airmass the aircraft is flying through. Modern jet aircraft with high bypass engines also have a distinctive buzz saw tone which is usually most audible during takeoff. This noise is caused by the interaction of the airflow with the fan blades at the front of the engine.
Factors that Affect Aircraft Performance
The level of noise generated varies according to aircraft size and type and can differ even for identical aircraft depending on factors such as weather conditions. Aircraft do not produce as much lift in hot weather when the air is less dense due to two factors. First jet engines produce less thrust because the air is less dense as the temperature increases. Secondly, the less dense air also affects the wing's ability to generate lift, which makes the wing less efficient and requires higher airspeeds to produce an equivalent amount of lift. Both of these factors cause planes to fly over the community at a lower altitude during climb out and require them to use more runway to become airborne.

Another major factor that influences aircraft noise is the weight of the aircraft, including passengers, baggage, cargo, and the amount of fuel onboard. When you make a trip in your family car, you don't worry about how much weight the car can carry. You fill up the gas tank and load up the bags and your family and drive off. In an airplane, you can't do that, as the plane won't be able to generate enough lift to overcome its weight and won't become airborne.
Every airplane type from a small single piston-engine Cessna 172 to a four-engined A380 has a certified Maximum Takeoff Weight (MTOW). This weight has been determined during the aircraft's initial type certification testing and is a hard number and is not to be exceeded by the pilots. This figure represents the absolute maximum weight the aircraft can weigh and still be safely guaranteed to fly. To help ensure the airplane doesn't exceed the MTOW pilots must make very precise calculations to determine how much fuel, passengers, and cargo can be safely transported.
All newly manufactured aircraft are weighed prior to delivery to the customer. This calculation establishes the empty weight of the aircraft which includes all interior fittings like seats, galleys, and restrooms. Adding crew weights to this figure establishes the Operating Empty Weight (OEW). This weight doesn't include passengers, cargo, or fuel. The OEW can vary from aircraft to aircraft based on the specific customizations chosen by the airline.

In the case of the example, Boeing 787-8 operated by American Airlines the empty weight of the airplane is 264,500 lb. and its maximum takeoff weight is 502,500 lb. This means that before a single passenger, bag, or drop of fuel is loaded more than 52% of the aircraft's maximum takeoff weight is already accounted for. This leaves 238,00 lb. available for a combination of fuel, passengers, and cargo that can be loaded. The maximum structural payload of 90,500 lb. refers to the maximum amount of passengers, bags, and cargo that can be safely carried by the airplane. Accounting for the maximum structural payload this leaves 147,500 available for fuel if the aircraft is loaded to its maximum structural payload of 90,500 lb. The airplane's empty weight plus its maximum structural payload is referred to as the maximum zero fuel weight. Boeing's 787-8 in American's configuration has a maximum fuel capacity of 223,378 lb. but with a full 90,500 payload, it's only possible to load 147,500 lb. of fuel onboard and still be below the aircraft's MTOW.
The largest single variable in an aircraft's takeoff weight is the amount of fuel needed to complete the flight to the destination. A gallon of Jet-A fuel weighs 6.8 lb. (3.1 kg.), which means that it doesn't take long for that weight to be a substantial contribution towards reaching the aircraft's MTOW. In some cases, in order to carry enough fuel to fly nonstop to the destination especially on hot days it may be necessary for the airline to weight restrict the flight. This means that the number of passengers, bags, and cargo must be reduced in order to decrease the aircraft's weight and bring it below the MTOW.
Take the example below of two identical Boeing 787-8 Dreamliners. Both are departing DFW Airport in Dallas, Texas. The first is bound for Los Angeles which is a relatively short 1,464-mile flight. The second is a trans-Pacific flight to Beijing, China which clocks in at 7,217 miles.

The amount of fuel required to reach both destinations is drastically different but not just because of the distance. The trans-Pacific flight must also meet minimum fuel requirements for trans-oceanic Extended-Range Twin-Engine Operational Performance Standards (ETOPS) flights established by the FAA and ICAO. These requirements include specific fuel reserves required for en route deviations, 45 minutes of airborne holding, fuel to conduct a missed approach to the runway, and after all that enough remaining to divert to an alternative airport if necessary. The FAA and ICAO also establish minimum fuel requirements for landing which are very strict and landing below this minimum level will immediately attract the interest of regulators. All of this must be calculated by the pilots prior to departure from the origin airport and they must also consider en-route wind conditions to determine if they will have a head or tailwind which also affects the amount of fuel needed for a particular flight. The fuel planning chart below details the specific fuel requirements for each flight.

The final aircraft weight is arrived at by adding the empty weight, payload, and fuel load required together. The taxi-out weight is the weight of the airplane when it pushes back from the gate. You might notice that the maximum taxi weight is 1,600 lb. more than the maximum takeoff weight. How is this possible? The maximum taxi weight is higher than the maximum takeoff weight because the assumption is that during taxi the aircraft will burn off the extra 1,600 lb. of weight in fuel to get to the runway.

Comparing the weights of the two flights there is a taxi out difference of 124,497 lb. which is the result of the much greater amount of fuel required to complete the scheduled 13 hours 19-minute flight to Beijing than that of the relatively short 2-hour 50-minute hop to Los Angeles.
Evolution of the Jet Engine
The Jet Age officially began on June 27, 1949, when the de Havilland company's DH 106 Comet took to the skies of Great Britain. The Comet was the world's first commercial jet and its introduction into commercial service would spark a revolution in the airline industry that would in a few short decades shrink the globe, greatly expand access to air travel, and link the countries of the world together like never before. With this technological progress and incredible speed came the side effect of increased noise for residents living around airports. This problem would eventually result in legislation by the International Civil Aviation Organization (ICAO) and Congress in the United States in an attempt to mitigate airplane noise and require aircraft and jet engine manufactures to reduce the noise levels of future jet aircraft.
The industry has made substantial progress since the first generation of jet airlines were introduced in the 1950s. Comparing the noise certification values of narrowbody transport aircraft over the last six decades as shown in the chart below reveals that today's generation of jets like the 737 MAX and A320neo are almost 30 decibels (dB) quieter than their first-generation cousins the Boeing 707 and Douglas DC-8.

This is very significant when you consider that a 30 decibel (dB) reduction in noise represents a 1,000x decrease in the sound energy between the 707 and A320 neo. To translate this to human hearing the average person would perceive the A320 neo to be about 1/8 as loud as the 707. This is due to the fact that sound energy is measured on a logarithmic scale with a 10 dB change in sound level representing a 10x increase or decrease in sound energy. By far the greatest contribution to the overall reduction in aircraft noise has been the introduction of successively quieter and more efficient jet engines.
The first generation of commercial jet engines widely used on early models of the Boeing 707, Douglas DC-8 and Convair 880 were straight turbojets. The first commercial turbojet aircraft to enter service was the de Havilland Comet 1 in 1952 which was powered by four Rolls-Royce H.2 Ghost 50 turbojets producing 5,000 lb. of thrust each.
This design is ideal for high-speed supersonic flight, where the turbojet can operate at maximum efficiency. A turbojet's main drawback is that it is extremely fuel-inefficient especially at the lower operating speeds which jet airliners typically fly at. They are also thrust limited, meaning that the engine thrust that can be produced is directly proportional to the amount of air ingested and the speed of the airflow through the engine (excluding afterburners). Since 100% of the air ingested into a turbojet is used in the combustion process the only way to increase engine power (thrust output) is to increase the flow of air into the engine which means the engine fan and turbine blades must spin faster to accelerate the airflow through the engine. This significantly increases the noise output of the engine, making them extremely loud.

The second generation of commercial jet engines, the low bypass turbofan engine, was first introduced on the Boeing 707-420 in 1960 which was powered by 4x Rolls-Royce RCo.10 low bypass turbofans producing 16,500 lb. of thrust each. A significant increase in thrust is possible with this engine design. Unlike turbojets where all the air ingested is used in the combustion process, in a turbofan engine not all of the air that flows into the engine enters the combustion chamber. Some of the air enters the engine and is accelerated by the fan blades at the front but bypasses the engine core and is expelled out the back mixing with the high-speed airflow from the jet engine core. The net result is that this bypass air which is only accelerated by a small amount compared to the core flow through the engine produces substantial additional thrust. This makes turbofans engines more fuel-efficient as they use much less fuel to produce higher amounts of thrust.
This design also reduces noise in two ways. First, the fan, compressor, and turbine blades don't have to spin as fast to produce the same level of thrust as a turbojet. Secondly, the lower speed bypass air envelops the high-speed jet exhaust from the core helping to reduce the noise output of the jet engine. The low bypass turbofan engine was used extensively on later models of the DC-8, 707 as well as the British Aircraft Corporation One-Eleven, Hawker Siddeley Trident, Vickers VC-10, Douglas DC-9, MD-80, Boeing 727, and 737-200 series among others. Early low bypass turbofans had a bypass ratio of 1:1, meaning for every 1 kg. of air that passed through the bypass duct, an equal 1 kg. of air flowed into the core and was used for combustion.

The third generation of jet engines, the high bypass turbofan engine was born out of a requirement by the U.S. Air Force in 1964 for a heavy-lift military transport that could carry cargo that wouldn't fit in the C-141 Starlifter. The aircraft design required a revolutionary new engine capable of producing over 40,000 lb of thrust. General Electric's TF-39 paired with Lockheed's C-5A Galaxy design won the competition, becoming the world's first high bypass turbofan engine to enter service.
Boeing who lost the competition quickly found a new application for its engine partner Pratt & Whitney's new high bypass turbofan when Pan American's Juan Trippe approached the company looking for an aircraft with twice the seating capacity of the airline's existing 707. The result was the Boeing 747-100, the world's first wide-body passenger jet, powered by Pratt & Whitney's JT9D-3A.
The high bypass turbofan engine is just what it sounds like, a turbofan with a much higher bypass ratio than first-generation low bypass turbofans. The JT9D was built with a 5:1 bypass ratio which allowed it to produce over 40,000 lb. of thrust per engine. When compared with its low bypass cousins like the JT8D and RCo.10 the fan diameter was more than twice as wide. The giant diameter of the fan and increased efficiency it delivered allowed the engine to produce a very large amount of thrust from the low-speed bypass air. The design also reduced noise as the majority of the thrust was generated from the low-speed bypass air. The first few generations of the high bypass turbofan engine were used extensively on the Airbus A300, A310, A320, Boeing 737 Classic, 747, 757, 767, Lockheed L-1011, McDonnell-Douglas DC-10, and MD11.

The fourth generation of jet engines introduced the very high bypass jet engine which first took to the sky in 1995 attached to the Boeing 777-200. The 777 was the first of a new generation of large twin-engine wide-body airliners designed to replace aging DC-10's, L-1011's, and compete with Airbus' duo of the twin-engine A330 and four-engined A340. To power, the 777 Boeing needed an engine that could produce over 90,000 lb. of thrust, more than double that of the first generation high bypass JT9D. The 777 was offered with engines from all three major engine manufacturers GE, Pratt & Whitney, and Rolls-Royce. General Electric's GE90-94B was the highest thrust engine of the group delivering 94,700 lb. of thrust with a 9:1 bypass ratio design and a fan diameter of 10 feet 3 inches, which is similar to the fuselage diameter of the 737.

By increasing the size of the engine and thus increasing the bypass ratio, the total thrust output was able to be increased substantially. Since a greater percentage of the engine's thrust was developed from the bypass airflow, this greatly reduced the amount of fuel needed and allowed for a substantial decline in the engine noise. The GE90 was further refined and improved for the later 777-300ER growth variant and the maximum thrust increased to an incredible 115,300 lb. The very high bypass turbofan engines are used extensively on the A340-500/600, A380 and Boeing 777.
The fifth generation of jet engines, the ultra-high bypass turbofan, first took to the skies attached to Boeing's 787-8 Dreamliner in 2009. Boeing's Dreamliner is powered by the Rolls-Royce Trent 1000 engine or General Electric GEnx, which produces between 64,000-76,000 lb. of thrust.
Ultra high bypass jet engines succeed in increasing the bypass ratio, while not significantly increasing the engine size. Comparing the first generation JT9D-3A which had a fan diameter of 95.6 inches and the Rolls-Royce 1000 which has a fan diameter of 112 inches you get a difference of roughly 17 inches, but an increase in thrust of over 25,000 lb.
The 777 demonstrated that there are practical limits to how far an engine can be increased in size before it won't fit safely under the wing, so in order to overcome these limitations engineers worked to reduce the internal engine cross-section by using advanced materials and introducing a more efficient architecture which utilized fewer parts and reduced the size of key components in order to increase the bypass ratio of the engine without drastically increasing the fan diameter. Ultra high bypass jet engines are used extensively on the Airbus A320neo, A350, and Boeing 777x and 787.
From its commercial debut in 1949 on the de Havilland Comet to the current generation the jet engine has seen numerous evolutions that allowed for dramatic leaps forward in fuel efficiency, huge increases in thrust while at the same time greatly reducing the noise of the aircraft they powered as illustrated in the chart below.

Aerodynamic Efficiency Gains
While larger, more fuel-efficient, higher thrust lower noise engines have been the main driver in reducing aircraft noise over the last six decades, there have also been significant gains made in improving the aerodynamic efficiency of successive generations of jet airliners which have contributed to the overall noise reduction of aircraft.
By far the largest area of efficiency improvements in the aerodynamic aircraft structure center around the wings. With each successive generation of commercial jets, manufacturers applied refined principles in the aerodynamic design, incorporated advanced technologies in manufacturing, and applied new lighter-weight materials. All of this combined to produce a lighter, stronger, more efficient aircraft. The wing is the most complex and important structure of an airplane. In designing a new airplane the engineers must consider the wing shape, thickness, sweep, and bend of the wing. All of these elements factor into how efficient the wing will be and what its lifting capacity will be.
Over the decades the wing design of commercial airliners has been refined to make them much more aerodynamic, increase their lifting capacity, and reduce the induced drag produced. These improvements have enabled newer aircraft to climb higher, faster, and transport more passengers and cargo over greater distances. New materials such as carbon fiber composites have further enhanced the lifting capacity of the wing, reduced structure weight, and airframe drag.
The graphic below illustrates the efficiency gains of the Boeing 737, the most produced commercial jet airplane in aviation history, through three and a half generations from the 737-200 Advanced in 1971, through to the 737-500 in 1990, and finally the 737-600 in 1998. The 737-500 was designed as a direct replacement for the 737-200, while the 737-600 was designed as a direct replacement for the 737-500. As is clearly shown in the graphic the length of the three aircraft from nose to tail remains virtually unchanged, but with each successive generation, the aircraft's wingspan grew incrementally.

The 737 Original series first entered revenue service in 1968 and was made up of three different models, the 737-100, 200, and 200 Adv. (Advanced). The shorter 737-100 saw a very short production run of only 30 aircraft, with the bulk of orders coming for the 737-200 and 737-200 Adv. The 200 Adv. model incorporated more powerful engines, greater fuel capacity, increased range, and small aerodynamic improvements. The original wingspan of 93 feet was the same between the 200 and 200 Adv. The 737-200 became the production standard starting in 1971 with all subsequent 737 deliveries being advanced models.
The 737 Classic series first entered revenue service in 1984 and was made up of three different models, the 737-300, 400, and 500 incorporated a newly designed wing which was 2 feet longer than the 737-200, and provided an aerodynamic improvement in the efficiency of 2.5%. The 500 series the smallest variant of the classic series was first delivered in 1990 to launch customer Southwest Airlines.
The 737 Next Generation series first entered revenue service in 1997 and was made up of four different models, the 737-600, 700, 800, and 900, and incorporated a redesigned wing which was 22 feet longer than that on the classic series and provided a 20% improvement in aerodynamic efficiency over the 737-500. The 600 series the smallest variant of the NG series was first delivered in 1998 to launch customer Scandinavian Airlines (SAS)
The 737 MAX is not included in the chart because due to low sales of the 600 model Boeing opted not to build a direct replacement as part of the 737 MAX family of aircraft which includes the 737 MAX 7, MAX 8, MAX 9, and MAX 10.
Aircraft Noise Certification
The FAA in cooperation with other regulatory bodies around the world working through the International Civil Aviation Organization (ICAO) regulates the maximum noise level that an individual civil aircraft can emit by requiring aircraft to meet certain noise certification standards.
The U.S. noise standards are defined in the Code of Federal Regulations (CFR) Title 14 Part 36 - Noise Standards: Aircraft Type and Airworthiness Certification (14 CFR Part 36). The FAA publishes certificated noise levels in the advisory circular, Noise Levels for U.S. Certificated and Foreign Aircraft.
The FAA Modernization and Reform Act of 2012, in Section 513, placed a prohibition on operating certain aircraft weighing 75,000 pounds or less not complying with Stage 3 noise levels, and on July 2, 2013, the FAA published a Final Rule in the Federal Registry for the Adoption of Statutory Prohibition the Operation of Jets Weighing 75,000 Pounds or Less That Are Not Stage 3 Compliant. Consequently, the operation of all non-military Stage I and II aircraft are currently prohibited in U.S. Airspace. Stage 3, 4, and 5 aircraft are currently allowed to operate in the U.S. without restrictions.
The current FAA Stage 5 Airplane Noise Standard went into effect on November 3, 2017, and applies to any person submitting an application for a new airplane type design with a maximum certified takeoff weight of 121,254 pounds (55,000 kg) or more on or after December 31, 2017; or with a maximum certified takeoff weight of less than 121,254 pounds (55,000 kg) on or after December 31, 2020.
The new Stage 5 noise standard requires a cumulative noise reduction of 7 (EPNdB) Effective Perceived Noise level in decibels below the Stage 4 noise standard. The previous Stage 4 noise standard required a cumulative reduction of 10 EPNdB below the Stage 3 noise standard.
To establish the certified noise level of a new aircraft type, during the airplane's initial type certification flight test program the plane is flown over specialized microphones placed at fixed distances from the runway. As shown in the graphic below, noise measurements are recorded at three specific locations to capture takeoff noise, landing noise, and sideline noise. The aircraft is flown at its certified maximum takeoff weight for the Takeoff and Sideline measurements and its maximum landing weight for the Approach measurement with flaps and landing gear deployed.
The maximum noise level permitted for a particular aircraft type to meet a specific noise stage, whether it be III, IV, or V is not a fixed number. Larger, heavier widebody aircraft are allowed to make more noise than smaller, lighter narrowbody aircraft and still be compliant with a particular noise stage.
The maximum noise level permitted per aircraft type is also not fixed across the three measurement points. Generally speaking, the maximum noise level allowed is the highest for the Approach measurement, with Sideline being the next highest and Takeoff being the lowest.
The approach phase of flight is when the aircraft is lowest to the ground as it descends on the final approach to the runway and takes into account the added airframe noise from the extended flaps, landing gear, and high engine power settings. The sideline measurement records the noise of the aircraft on its takeoff roll and very initial climb away from the runway. The Takeoff measurement is captured under the departure path of the plane when it is climbing away from the airport with the landing gear retracted, and while the flaps are in the process of being raised. The airplane is the greatest distance away from the ground at this measurement point relative to the Approach and Sideline measurements which help explain why the maximum noise level allowed is lowest at this point.
As shown in the graphic below to derive the noise margin below the Stage IV limit, the measured noise level at each of the three measurement points (Approach, Sideline, and Takeoff) is subtracted from the maximum noise limit allowed for a particular aircraft at each measurement point. This process establishes the aircraft type's margin below the Stage IV limit at each measurement point. To calculate the aircraft's cumulative margin below Stage IV, the individual margins for all three points are added together.

The French Dirección General de Aviación Civil (DGAC) maintains a publicly accessible Noise Certification Database that contains the noise levels of airplanes certified according to ICAO regulations, Annex 16, Chapters 2, 3, 4, and 14 or according to FAA FAR 36, Stage 3, Stage 4 and Stage 5. Users can search by a number of categories including manufacturer, aircraft type, engine type, noise chapter/stage, and the aircraft's maximum take-off weight (in kg) if known. The database will pull the specific noise certification datasheet for the aircraft or export the data directly to a spreadsheet for further analysis.
For example N570AS a Boeing 737-800 with CFM56-7B24 engines and scimitar winglets operated by Alaska Airlines a frequent visitor to SJC.

This particular aircraft has a Maximum Takeoff Weight (MTOW) of 174,200 lb. (79,016 kg.) and a Maximum Landing Weight (MLW) of 146,300 lb. (66,361 kg.). Based on this information the database returns BOEING_10492 Noise Certification Datasheet for this aircraft type.
Aircraft are also classified by ATC for purposes of maintaining proper separation between dissimilar weight aircraft during the landing and takeoff phases of flight. All aircraft much like boats moving through the water creates a wake as they pass through the air. The larger and heavier the aircraft the bigger the wake they create. An aircraft's wake produces significant turbulence behind it especially from the wingtips, which generate lateral spiraling columns of air which are caused when the airflow under and over the wing converges at the wingtip. These spinning columns of air as illustrated in the picture below can flip a lighter aircraft over or send it out of control if it's following too closely behind the heavier airplane. The FAA publishes guidance to pilots on avoiding wake turbulence hazards in Advisory Circular 90-23G.
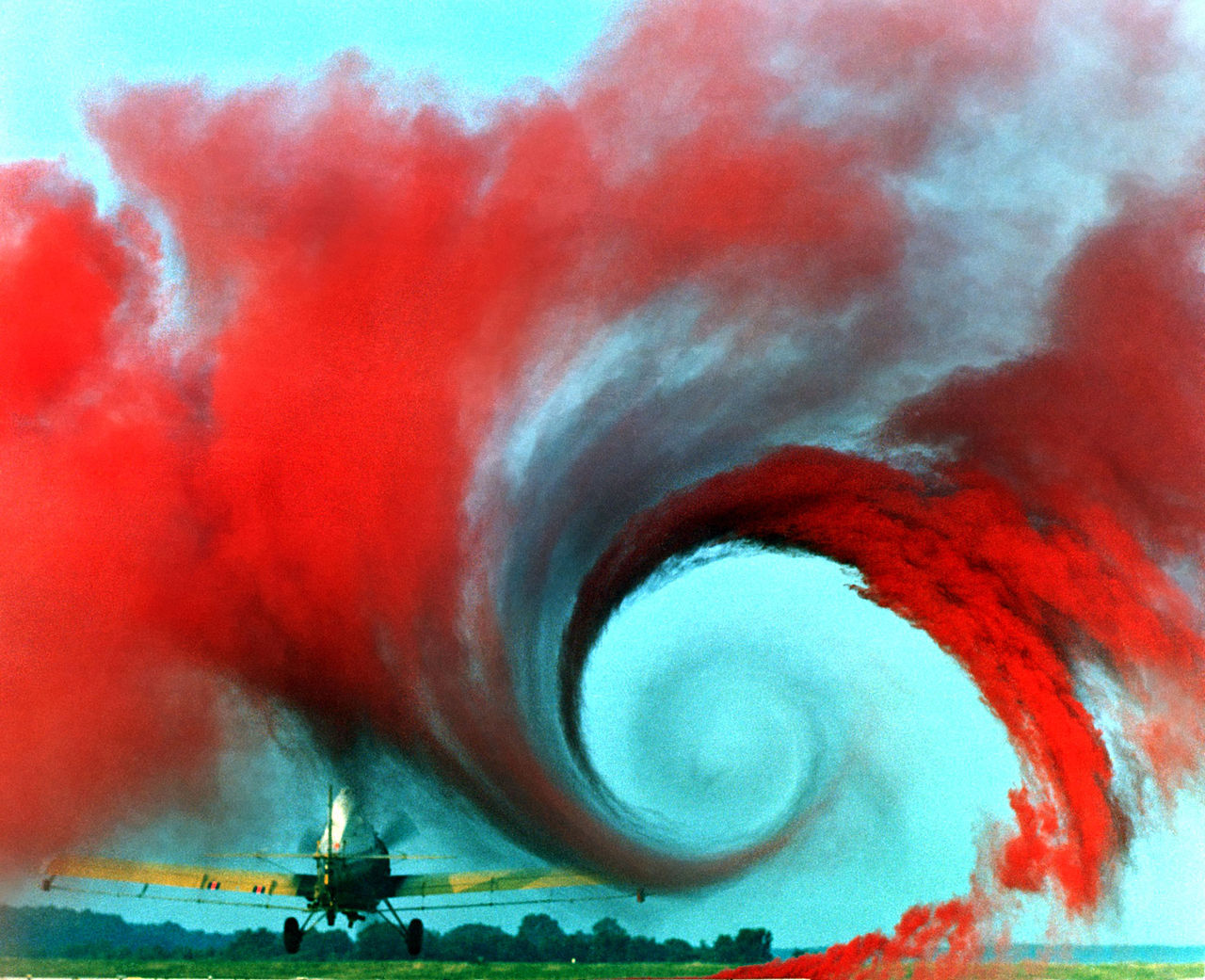
To avoid this the FAA developed minimum separation distances for aircraft based on their Maximum Certified Gross Takeoff Weight (MCGTOW). Under the old rules, aircraft were divided into four categories:
- Small (MTOW < 41,000 lb.)
- Large (41,000 lb. < MTOW < 300,000 lb.)
- Heavy (300,000 lb. < MTOW)
- Super (A225 and A380)
These rules while effective in greatly reducing the number of wake encounters, resulted in greater than necessary separation distances, especially between heavy aircraft. This inefficiency reduced airspace throughput and resulted in unnecessary delays.
To address these shortcomings the FAA in 2012 began a pilot project at Memphis, Tennessee (KMEM) which retained the previous weight categories but also addressed differences in approach speeds and wing configuration between aircraft. The project resulted in six categories of aircraft, with revised spacing requirements between aircraft classes, which increased capacity by 15% and saw average taxi times for FedEx, Memphis' largest carrier with over 500 operations a day reduced by three minutes.
The success of the pilot program resulted in an expanded program known as RECAT Phase I which introduced 6 static wake turbulence categories which considered MTOW, MLW, wingspan, and approach speeds. In total 61 aircraft types were included which represented about 85% of operations from 5 U.S. and 3 European airports. By April of 2016 RECAT Phase I had been implemented at 10 TRACON and 17 airport locations in the United States.
RECAT Phase II focused on a larger cross-section of 123 aircraft types which together made up 99% of U.S. air traffic at 32 U.S. airports. The largest change from Phase I to II was the shift from defining separation by wake turbulence category, but considering individual aircraft pairs of aircraft types such as (Boeing 747-400 leading an Airbus A321) when establishing minimum separation distances. The charts below demonstrate how the spacing in nautical miles between types on approach to land changed as a result of RECAT, with the first chart showing the old spacing requirements and the second chart the newly revised requirements.
Preceding Aircraft | Following Aircraft | Minimum Separation |
---|---|---|
HEAVY | HEAVY | 4.0 NM |
HEAVY | MEDIUM | 5.0 NM |
HEAVY | LIGHT | 6.0 NM |
MEDIUM | LIGHT | 5.0 NM |
Leader/Follower | A | B | C | D | E | F | G | H | I |
---|---|---|---|---|---|---|---|---|---|
A | -------- | 4.5 NM | 6.0 NM | 6.0 NM | 7.0 NM | 7.0 NM | 7.0 NM | 7.0 NM | 8.0 NM |
B | -------- | 3.0 NM | 4.0 NM | 4.0 NM | 5.0 NM | 5.0 NM | 5.0 NM | 5.0 NM | 6.0 NM |
C | 3.5 NM | 3.5 NM | 3.5 NM | 5.0 NM | 6.0 NM | ||||
D | 3.0 NM | 4.0 NM | 4.0 NM | 5.0 NM | 5.0 NM | 5.0 NM | 6.0 NM | 6.0 NM | |
E | 4.0 NM | ||||||||
F | 4.0 NM | ||||||||
G | |||||||||
H | |||||||||
I |
The FAA issued updated wake turbulence separation guidance on September 28, 2019, published in FAA Order JO 7110.126A. The updated standard in addition to MTOW also takes into consideration, landing speeds, wingspan, and ability to withstand a wake encounter. The new guidance gives ATC more flexibility in managing wake separation between aircraft. The table below illustrates the new FAA aircraft wake vortices classification system currently in place and the ICAO aircraft tyes that fit within each category.
A - Super | B - Upper Heavy | C - Lower Heavy | D - Non-Pairwise Heavy | E - B757 | F - Upper Large | G - Lower Large | H - Upper Small | I - Lower Small | |||
A388 | A332 | A306 | A124 | B752 | A318 | C130 | AT43 | E170 | ASTR | BE10 | |
A225 | A333 | A30B | A339 | B753 | A319 | C30J | AT72 | E45X | B190 | BE20 | |
A343 | A310 | A342 | A320 | CVLT | CL60 | E75L | BE40 | BE58 | |||
A345 | B762 | A3ST | A321 | DC93 | CRJ1 | E75S | B350 | BE99 | |||
A346 | B763 | A400 | B712 | DC95 | CRJ2 | F16 | C560 | C208 | |||
A359 | B764 | A50 | B721 | DH8D | CRJ7 | F18H | C56X | C210 | |||
B742 | C17 | AN22 | B722 | E190 | CRJ9 | F18S | C680 | C25A | |||
B744 | DC10 | B1 | B732 | GL5T | CRJX | F900 | C750 | C25B | |||
B748 | K35R | B2 | B733 | GLEX | DC91 | FA7X | CL30 | C402 | |||
B772 | MD11 | B52 | B734 | GLF5 | DH8A | GLF2 | E120 | C441 | |||
B773 | B703 | B735 | GLF6 | DH8B | GLF3 | F2TH | C525 | ||||
B77L | B741 | B736 | MD82 | DH8C | GLF4 | FA50 | C550 | ||||
B77W | B743 | B737 | MD83 | E135 | SB20 | GALX | P180 | ||||
B788 | B74D | B738 | MD87 | E145 | SF34 | H25B | PAY2 | ||||
B789 | B74R | B739 | MD88 | LJ31 | PA31 | ||||||
C5 | B74S | MD90 | LJ35 | PC12 | |||||||
C5M | B78X | LJ45 | SR22 | ||||||||
BLCF | LJ55 | SW3 | |||||||||
BSCA | LJ60 | ||||||||||
C135 | SH36 | ||||||||||
C141 | SW4 |
Takeoff separation distances are predicated on the average time it takes for wingtip vortices to dissipate making it safe for a lighter aircraft to takeoff behind a heavier aircraft on the same runway or a parallel runway separated by less than 2,500 feet. The time required between takeoffs of different aircraft classes are listed below and are based on the following aircraft taking off from the same point on the Runway as the preceding aircraft.
- Category B, C, D, E, F, G, H, or I aircraft departing behind Category A aircraft - 3 minutes hold time time
- Category B, C, D, E, F, G, H, or I aircraft departing behind Category B or D aircraft - 2 minutes hold time
- Category E, F, G, H, or I aircraft departing behind Category C aircraft - 2 minutes hold time
In addition to the separation standards both ATC and pilots of Category A-D airplanes use the suffix "Super" or "Heavy" when communicating with controllers via the radio. This lets the controller and other pilots know that the airplane is a Super (Category A) or Heavy (Category B, C or D) and they should exercise caution when flying behind them and maintain a safe separation distance in trail. For example UAL102 Heavy turn left heading three-four-zero degrees. The Aircraft Type Table lists common aircraft types you will spot in the skies over the Bay Area.